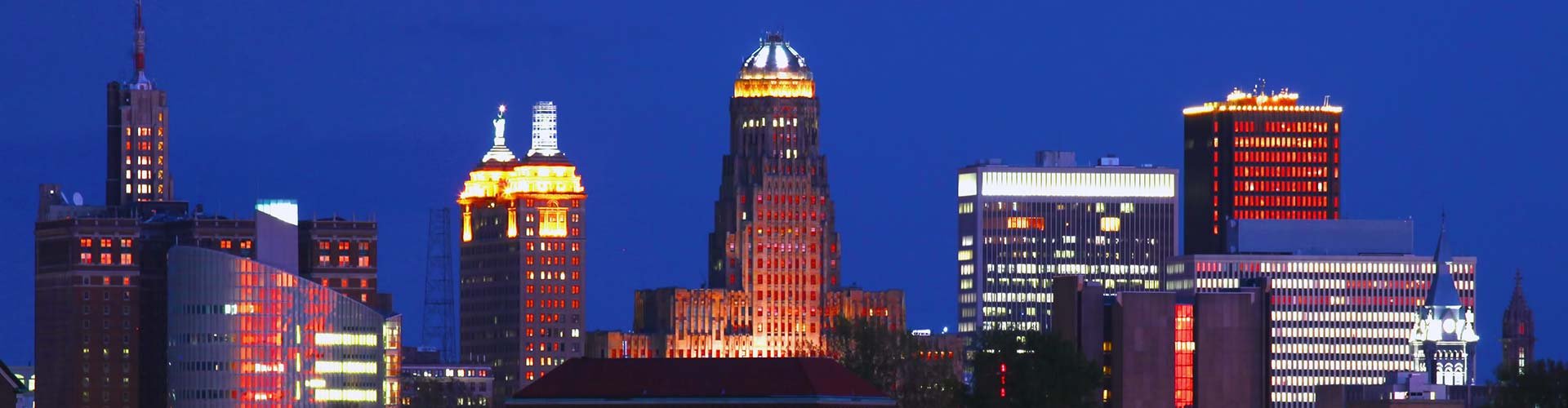
Production Machined Component Experts in Buffalo, NY
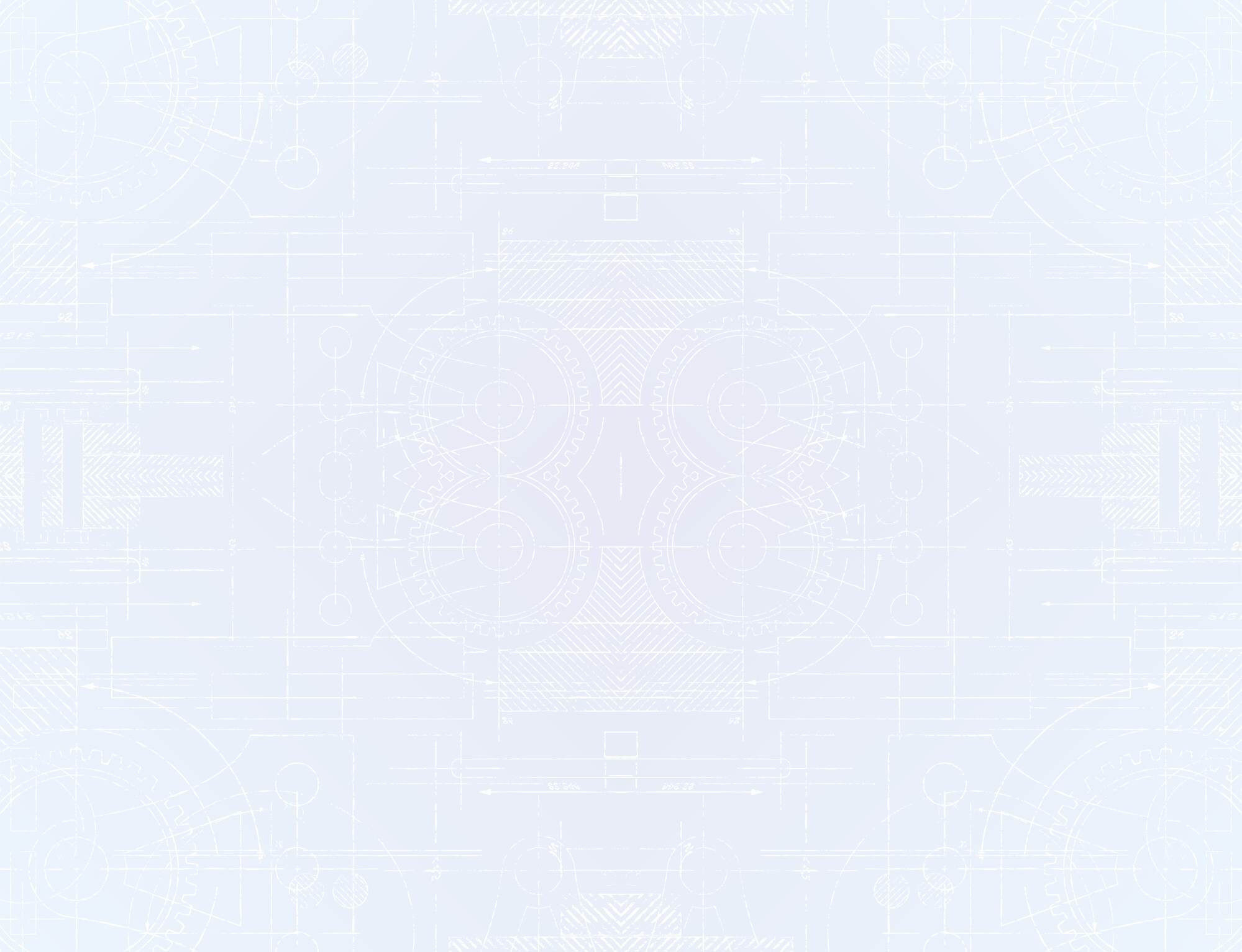
Specializing In Components for The Valve Industry
ISO 9001:2015 Certified | Dedicated to Excellence | Swiss Machining Capabilities
Serving Buffalo NY with Production Machining Services
Our proximity to Interstate 90 enables us to quickly and inexpensively reach your locations in Buffalo and throughout Western New York.
-
CNC Turning
-
CNC Milling
-
Grinding
Blending Experience in Machining and Grinding with Innovative Valve Part Manufacturing Solutions in Buffalo, NY
Ripley Machine Is an ISO 9001:2015 certified machine shop near Buffalo, New York area in operation since the 1950s. Ripley Machine has consistently modernized and incorporated technology, becoming a leader in machine efficiency and precision. In 1994, Quentin Bensink purchased Bornand Company and incorporated the company as Ripley Machine and Tool Company, Inc. Quentin continued to own and expand the business for the next 21 years. In 2012 Quentin was joined in management by his grandson Andrew Reinwald. In January of 2015, Andrew purchased the company from Quentin and became President. Quentin remained with the company through 2017 as an integral part of guidance for Andrew as the business transitioned ownership. Andrew remains committed to the core Christian values that Quentin operated the company through while continuing to explore opportunities to expand and develop the company. Andrew remains committed to the positive impact that the business can have on others through employment and charitable contributions.
Precision CNC Milling and Turning Serving Clients In Buffalo
A Buffalo area OEM came to our ISO certified machine shop looking for a solution to a cast iron valve body that they needed machined. They were having delivery and quality issues with their current machining supplier and had orders that were past due to their customer due to the issues. Our team immediately recognized that it would be a fit for our shop. Our team traveled to meet with the OEM to learn the end use of the cast valve body and the critical features of the body. We then utilized our shop ERP to adjust machine schedules to get these parts on our machine schedule without disrupting other promised delivery dates. Our team was able to repurpose some other tooling and fixtures to begin machining the castings within one week of the OEM initially contacting us.
Not only were we able to quickly begin machining the cast iron valve bodies, we were able to utilize automation to efficiently machine the bodies in two operations instead of four. Our CNC Lathes with live tooling were able to machine the first operation and drill and tap a side port on the body. We were then able to utilize our Kitamura HX-300iG CNC Horizontal Mill to machine two other sides of the valve body in one operation.
While our machining team was working on planning and the beginning stages of machining, our quality team was working diligently to setup in process checks and inspection requirements to ensure that there were no quality defects. We utilized our ERP to create detailed inspections instructions so any team member that was tasked with working on the parts would know exactly how they were expected to inspect the parts. To this day, we have continued to machine these valve bodies for this OEM and we have yet to have any defective products ship.
This project was a great example of how the Ripley Machine team is setup to provide high quality parts on-time to the entire Buffalo area.
Precision Centerless and Internal Grinding Services
Ripley Machine’s grinding services have been utilized by manufacturers in the Buffalo area for years. We work with Buffalo area machine shops of all size to provide ISO Certified Grinding services.
Our centerless grinding services have been utilized by numerous machine shops in the Buffalo area for years. We recently received a call from a customer in the Buffalo area that had a project that required centerless grinding after machining and heat treat. Our customer had numerous delays in obtaining material and during the machining and heat treat operations. They were well behind from their initially anticipated delivery date and were in jeopardy of causing delays with their customer. Our team worked to have multiple grinders setup before we received parts. Our customer dropped the parts off at our facility in the morning and we ground and delivered several thousand parts the same afternoon. While we prefer to stick to our normally promised two week lead times for grinding, this project is an example of what the Ripley Grinding Team is capable of!
It is the goal of Ripley Machine and Tool Company to focus on continuously improving and developing new business avenues so that we are can positively impact the lives of our employees and their families, our customers and our community. By developing a close working relationship with our customers we understand their requirements, and can often ‘fill in the blanks’ and make recommendations to improve the manufacturability of their parts, which saves them time and expense. We encourage you to check out our blog to learn more about how we are working diligently to improve our business and how we serve our customers.
Manufacturing Capabilities
CNC Turning
CNC Swiss Turning from .125" diameter to 1.250" diameter
Bar Feeding Capabilities from ½” to 3-1/2” diameter
Chucking Capabilities from ½” to 12” diameters
Live Centers (Including Face Driving Centers)
Live Tooling Capability
Indexing Chucks
Centerless Grinding
Bar Grinding from .062” to ¾” diameter on bar stock up to 14’ in length
Through Feed Grinding on parts from .062” to 3” diameter up to 6” in length
Infeed Grinding on parts from .062” to 3” diameter up to 6” in length
Pin and Shaft grinding up to 5” diameter and 10” in length
We are able to help meet our customers demands with these services:
Prototype to Production Batch Sizes- We can handle lot sizes from 1 part up to 1 million parts!
Just-in-Time Delivery
Blanket Release and Stock Programs
Incentive Pricing
Material and Casting Storage (controlled environment)
CNC Drilling and Milling
42” x 24” Table 3-Axis Mills, primarily used as Support Equipment for CNC Turned Product
Internal Grinding
Straight or Tapered Bore
¾” dia. bore up to 8” diameter bore on lengths up to 6”
Bluing Strips provided for all Taper Bores
Center Grinding
CNC Center Grinding on parts up to 20” Long
Additional Services
Qualified Vendors for Heat Treating, Plating, Screw and Swiss Machining, Assembly, Testing, Etc.